Cutting Consumables - cutting wheels
- Product Feature
- NASTON Cutting Wheel
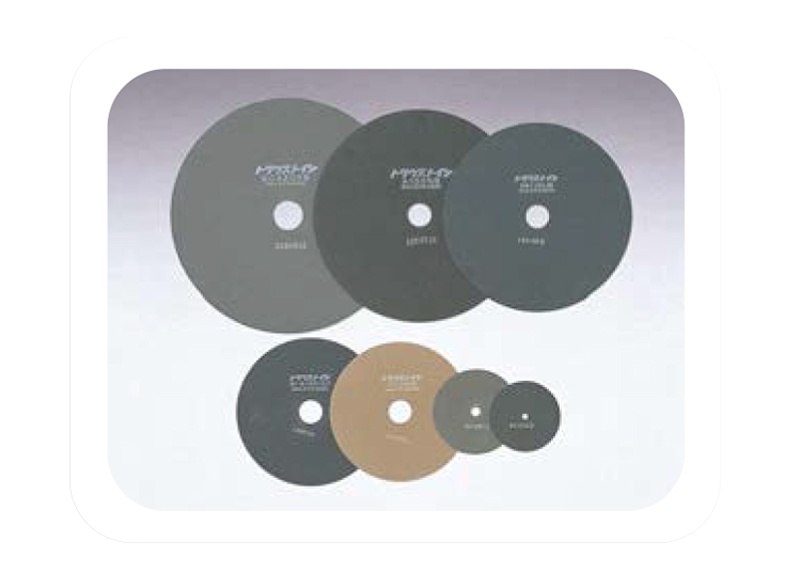 |
Processing with NASTON A type of precision processing method where a cutting wheel spinning at high speed is used to grind the material being processed via the extremely hard particles (abrasive grains) which the wheel consists of. The material can be gently processed without being damaged, while the superior precision cutting realizes a finely finished surface. |
Characteristics
- Utilizes extremely hard mineral grains and hence, in addition to ordinal metal materials and hard brittle materials such as hardened steel and cemented carbide/ceramics can be cut.
- Excellent finish and superior size precision are realized by the extremely fine grinding process.
- The cutting speed is extremely high, thus making the overall cutting efficiency (volume of chips ground per hour high even though the size of the chips is very small.
|
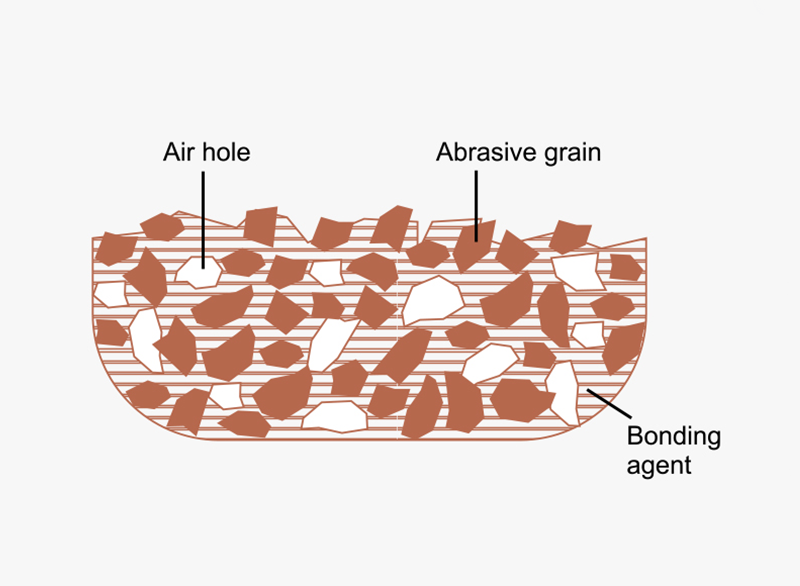 |
Mechanism The body of the cutting wheel, as revealed by the illustration on the left, consists of 3 elements abrasive grains, bonding agent, and air holes. The large number of abrasive grains on the working surface grinds the material away little by little because of their roughness. The abrasive grains gradually dull, get crushed and eventually come away from the working surface. However, as grains fall off new abrasive grains sequentially appear on the surface. This means that the edge of the wheel remains at the end, although the external diameter does decrease in size. |
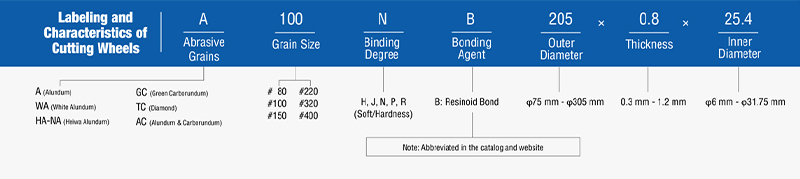
 |
 |
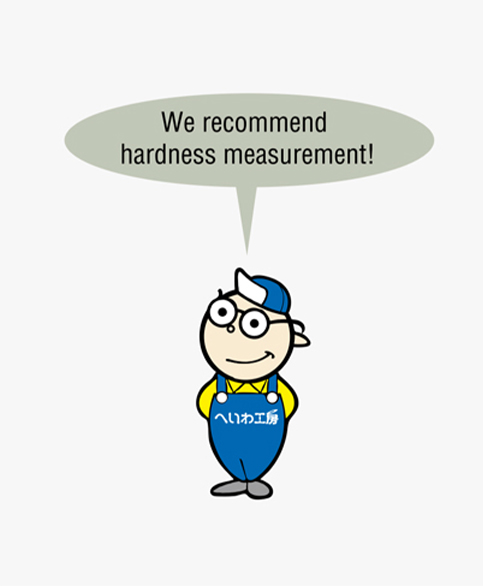 |
Helping selection of CuttingWheels By measuring the workpiece's hardness, it is possible to estimate the mechanical properties such as the material's strength and durability. By checking the hardness, it is possible to select the optimum abrasive grain and binding degree. So that it is possible to prevent the breakage of the workpiece and cutting wheel at the time of cutting, making for ideal cutting.
Note: The table displays the hardness comparison based on the Rockwell hardness (HRC) and Vickers hardness (HV) |
φ150-230
φ225-305